Wind power
We help you get the best out of composites
If you are thinking about longer blades or how to ensure higher uptime, so are we. We’ve been working with wind energy OEMs for several decades, helping to take advantage of the benefits that composites provide.
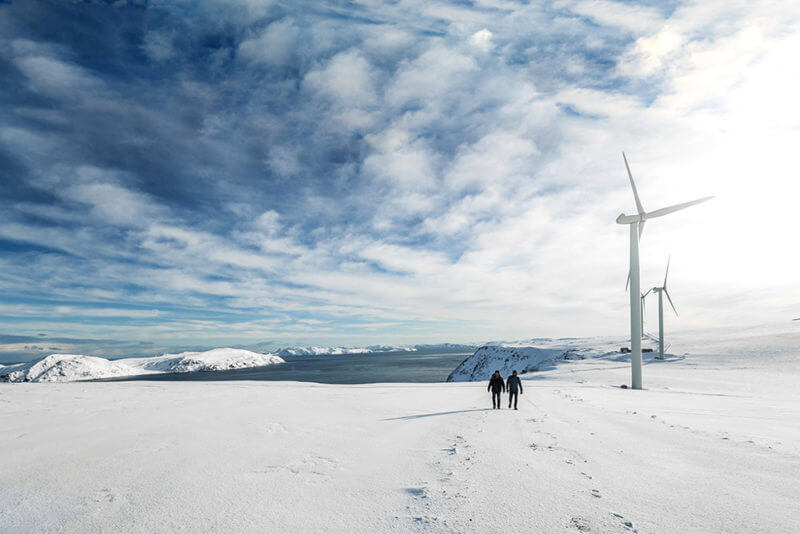
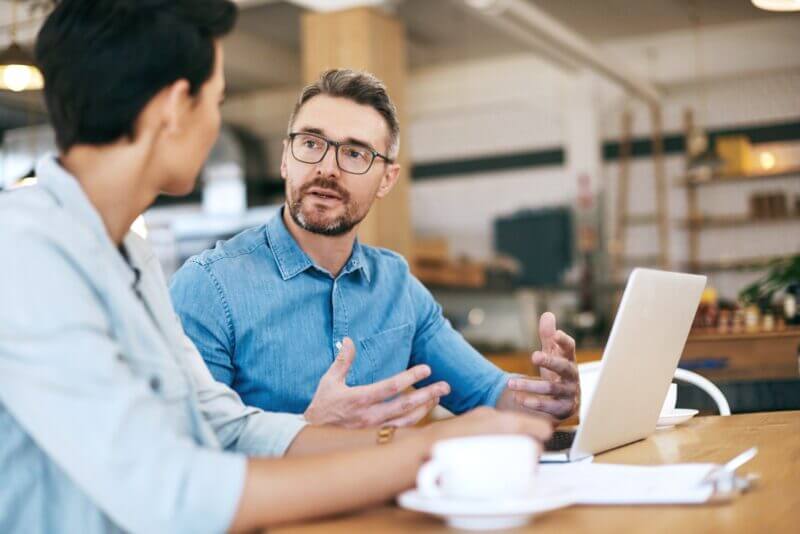
Make us your wind energy partner
Global presence
Our global footprint and manufacturing capacity allow us to follow you and deliver around the world and even provide you with redundant manufacturing capabilities.
Collaborative R&D
We have over 25 years’ experience in the wind energy business and we truly value the collaborative relationships between our engineers and yours.
Cost efficiency focus
We understand how to use carbon fiber in the most cost-efficient manner to meet cost, weight, and strength requirements.
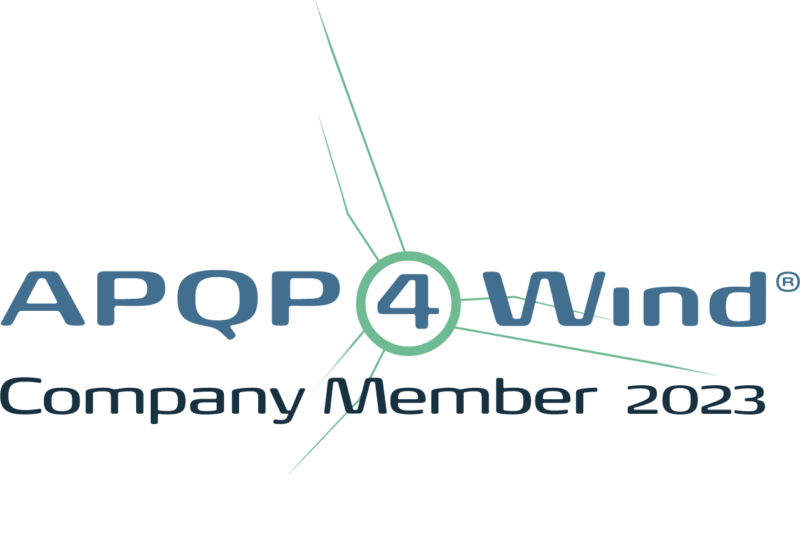
We are an APQP4Wind Member Company for all our wind production sites. APQP4Wind is a non-profit organization founded by world-leading wind turbine manufacturers and suppliers, focusing on continuous quality improvement for the wind industry. The APQP4Wind quality assurance methodology is designed to reduce risk and lower the costs of poor quality, with the aim of achieving a levelized cost of energy for the wind sector. Learn more abut the organization here >>
We offer more than just products
Let us add more value with additional fabrication or secondary processing in our factory. We offer services to cut, chamfer, mill, and even create custom kits. This saves you time and reduces your supply chain complexity.
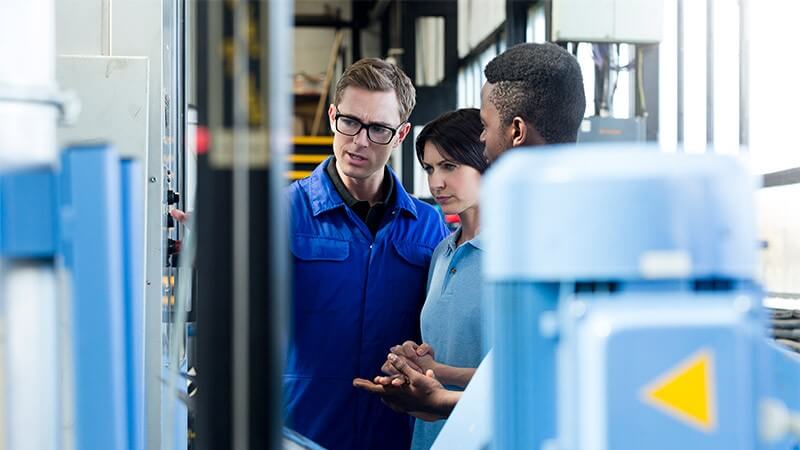
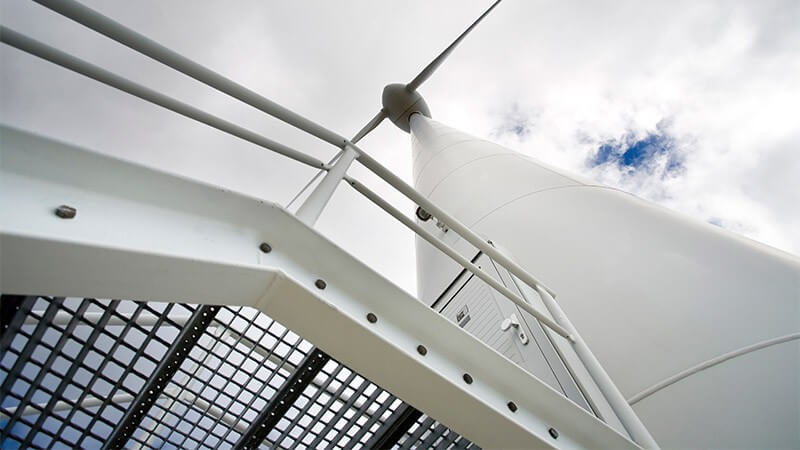
How composites are used in wind turbines
Composites, such as fiberglass and carbon fiber, are used as reinforcing materials in several wind applications. Their high strength and stiffness characteristics combined with their low weight and design flexibility make them perfect materials for turbines. You can find composites in blade reinforcements, blade laminates, spar caps, blade root joints, spacers and carrots, for example. Additionally, composites are used in access structures (such as ladders and platforms), as well cable management systems and even as in the generator itself as insultation solutions. We manufacture fiberglass and carbon fiber solutions for all of these areas.
Why composite manufacturing technology matters
Over the past decades you can see the power increases and designs of wind turbines evolve. No matter what the turbine design, the end goal is always the same: make wind energy more cost efficient and increase turbine operational life cycles.
Because of this each of the turbine’s component and solutions needs to focus on cost efficiency and durability. This sets high standards for quality expectations and the need for suppliers to ensure volume deliveries.
That’s where our experience and expertise with continuous manufacturing technologies of pultrusion and pull-winding really benefit our wind customers. We focus on using the raw materials, such as carbon fiber, in the most cost-efficient manner both in the design of your solution and in the manufacturing processes.
Efficient pultrusion and pull-winding help ensure consistent quality while reducing production waste and scrap. They also offer many design and material design possibilities.
Benefits of using composites
Light weight
They help reduce blade weight and increase length without compromising stiffness and strength.
Optimize blade performance
Using carbon fiber blade reinforcements help you design longer, lighter, and more efficient blades.
Cost-efficient solutions
Our continuous manufacturing technology delivers high-quality, high-volume deliveries.